——Low Oil Temperature: Servo motor only works when necessary, decreases system oil temperature and saves cooling water consumption effectively.
——High Energy efficiency: In condition of ideal working state, power consumption is 20%-80% less than that of traditional fixed pump, saving the energy effectively.
——Fast Response: With stable performance, servo motor control system is equipped with precise pressure feedback device, improving motion response and production efficiency.
——Low Noise: Different from traditional fixed pump system, servo machine is only works when necessary, offering you a quieter working place with less noise.
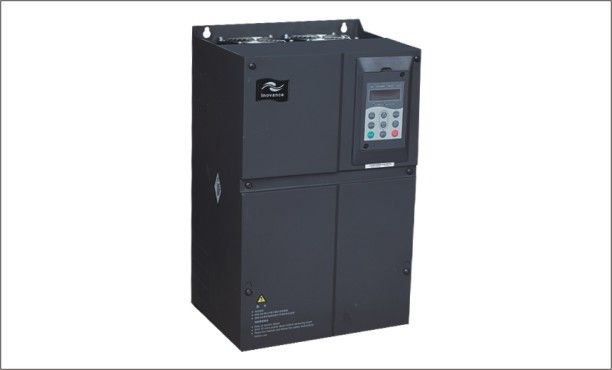
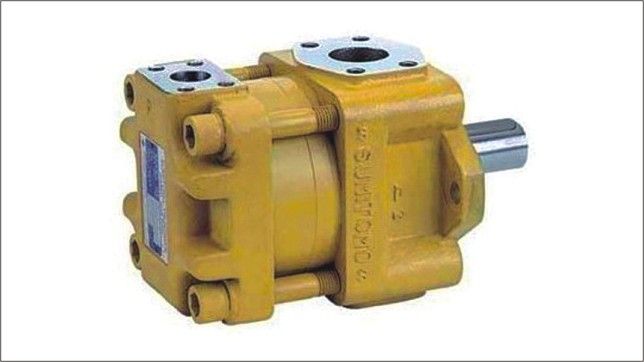
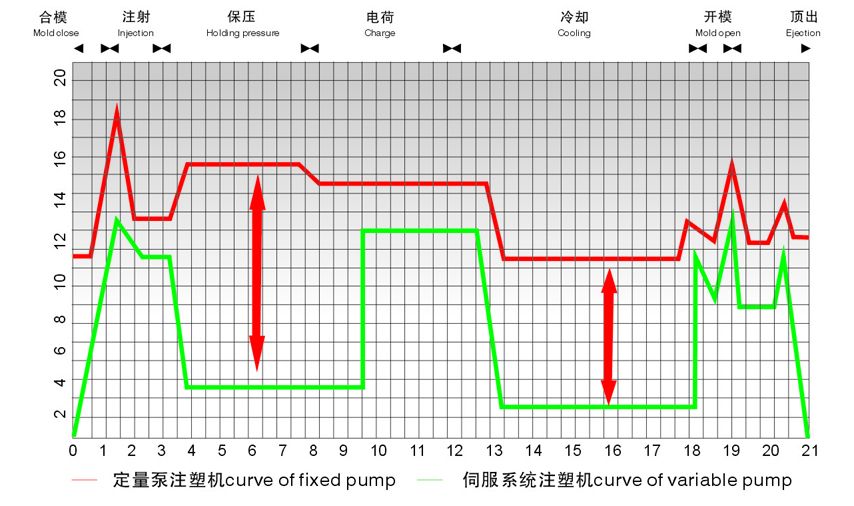
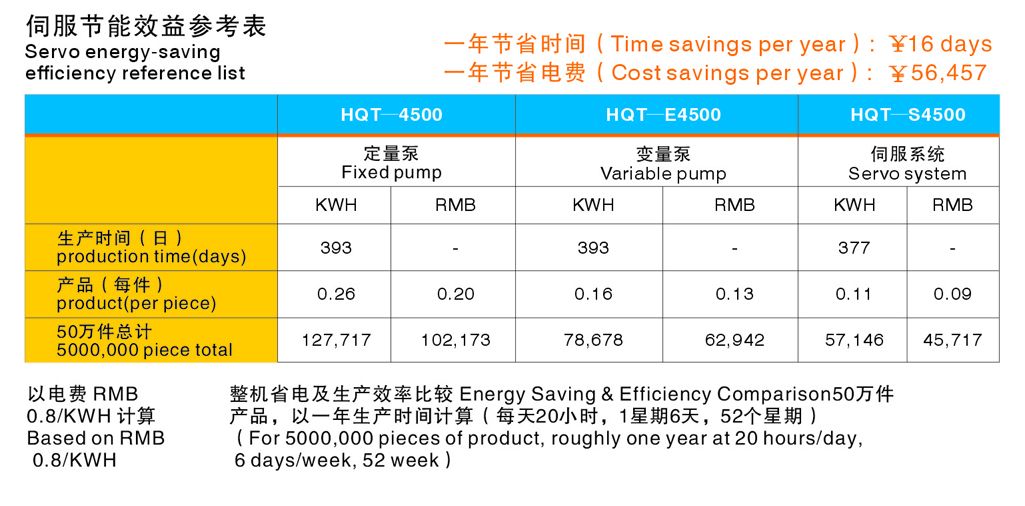
Variable pump machine
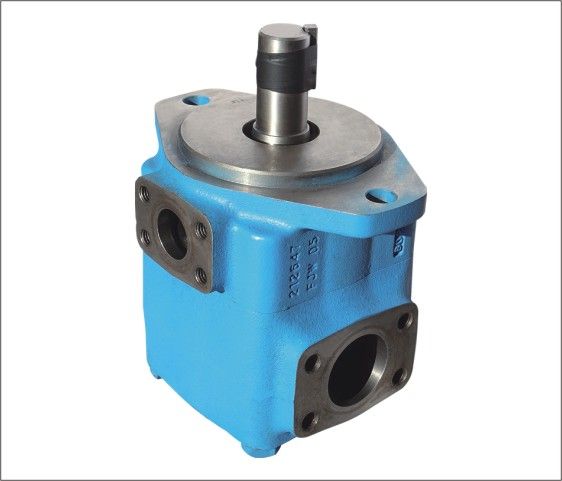
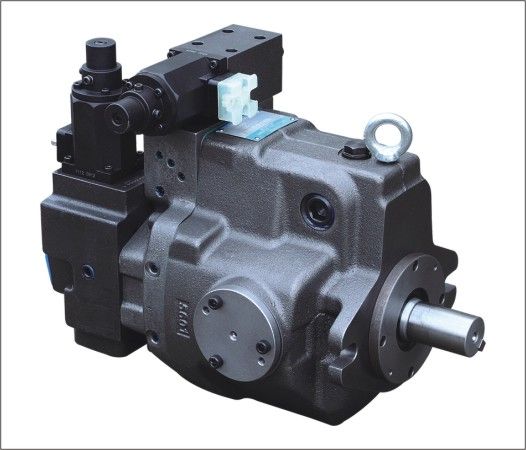
1、 Energy Saving: In the ideal working state, power consumption is 30%-60% less than that of ordinary fixed pump, saving the energy effectively.
2、 Oil Saving: Provided with imported high quality oil filter, longer life of hydraulic oil.
3、 Water Saving: Without overflow heating, low oil temperature saves cooling water and prolongs the service life of sealing parts.
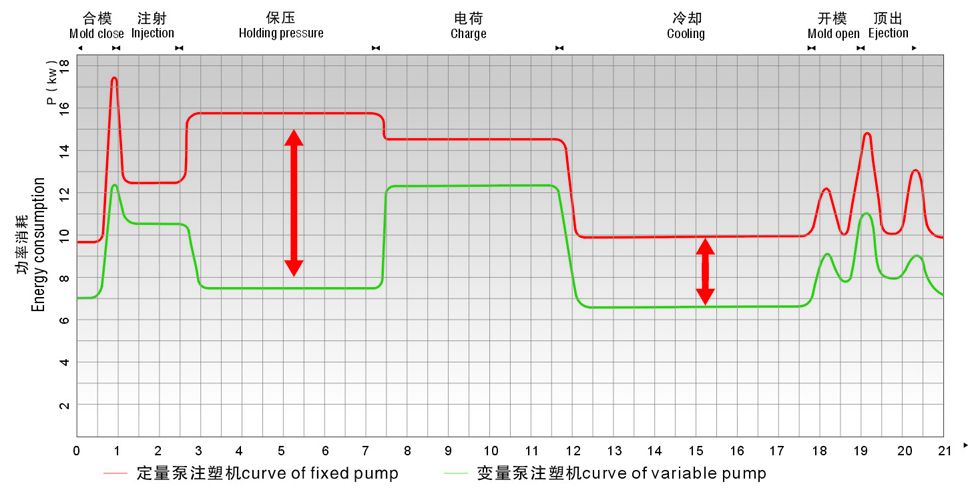
Item |
UNIT |
HQT1280 |
INJECTION UNIT |
|
A |
B |
C |
Screw Diameter |
mm |
36 |
40 |
45 |
Screw L/D Ratio |
L/D |
22.2 |
21 |
18 |
Shot Volume(Theoretical) |
cm3 |
184 |
227 |
288 |
Injection Weight(PS) |
g |
168 |
207 |
262 |
Plasticizing Capacity(PS) |
g/s |
10.6 |
13.0 |
16.0 |
Injection Rate |
g/s |
86 |
106 |
134 |
Injection Pressure |
Mpa |
222 |
180 |
142 |
Screw Speed |
r/min |
187 |
187 |
187 |
CLAMPING UNIT |
|
|
Clamp Tonnage |
KN |
1280 |
Toggle Stroke |
mm |
350 |
Space Between Tie Bars |
mm |
410×410 |
Max.Mould Height |
mm |
430 |
Min.Mould Height |
mm |
150 |
Ejector Stroke |
mm |
120 |
Ejector Tonnage |
KN |
38 |
Ejector Number |
pc |
5 |
OTHERS |
|
|
System Pressure |
Mpa |
16 |
Pump Motor Power |
KW |
13 |
Heater Power |
KW |
9.3 |
Machine Dimension(L×W×H) |
m |
4.29×1.42×1.84 |
Oil Tank Capacity |
L |
240 |
Machine Weight |
T |
4.2 |
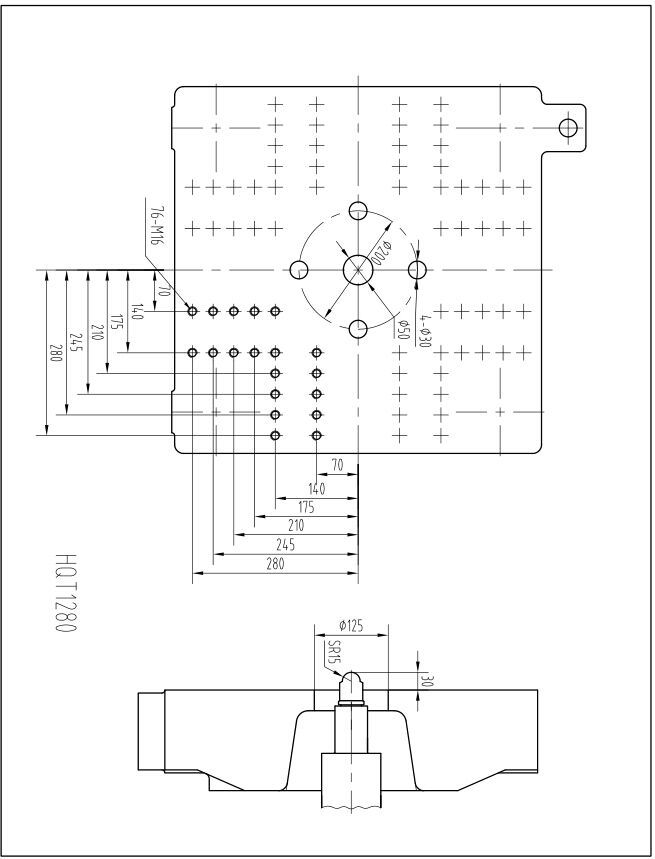
Control System
1.New generation of CPU, with high precision, stability and intelligence;
2.Automatic fault diagnosis and alarm system
3.PID control and display of barrel temperature
4.Multi-stage control of ejection and core pulling
5.Production data storage and printing outlet function;
6.Injection speed and pressure display
7.High oil temperature protection and automatic power breakoff
8.EUROMAP robot interface
9.Remote control and network monitor function Big LCD colar screen, Program multi-language support High-speed, precise electronic sensor NOVO imported from Germany, makes the position control accurate.
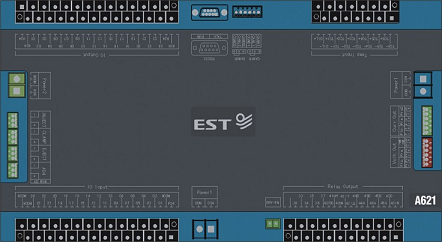
Hydraulic System
1.World famous brands of hydraulic pump and valve, make movement of machine accurate , reliable and saving energy.
2.Imported sealing parts is more durable, and of better elasticity.
3.Simples and clear oil pipe allocation, reduces energy lost and easy for maintenance.
4.Unique hydraulic circuit design with larger heat dissipation surface and low noise, reduces cooling water consumption and prolongs service life of sealing elements.
Injection System
1.Parallel Double-cylinder injection system ensures steady injection motion, avoids barrel distortion and leakage from unbalanced force; Thus, it extends life of screw and barrel, improves plasticizing effect.
2.Multi-stage injection speed and pressure control are suitable for different complexed thermoplastic molding process;
3.For every machine model, 3 or 4 nitrided bimetal screw & barrel of various diameters and special design are provided, to satisfy requirement of different material and product.
4.Integral design of injection unit has advantages of compact structure , light weight, good rigidity and reliability.
5.Differential injection process with accelerating rod, reduces resistance force and makes injection smooth and fast.
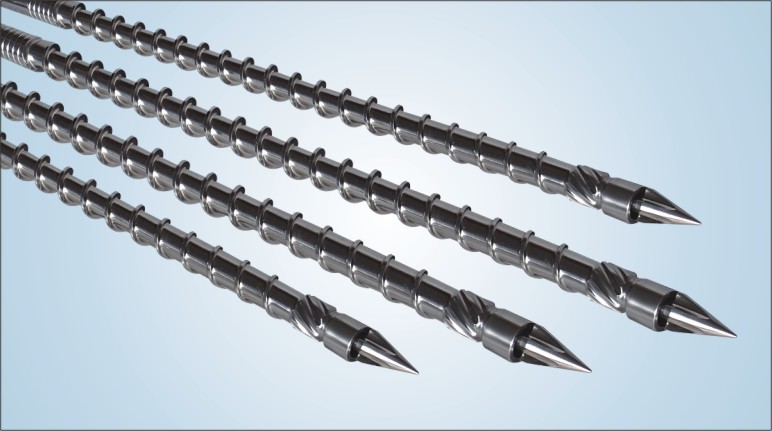
Clamping System
1.Five point double toggle clamping unit, linkage structure of connecting rod guarantee high rigidity and accuracy of mechanic system.
2.Reinforced platens with T slot, larger open stroke and mold space, make mould installation easier.
3.Multi-stage clamping pressure & speed control, and Fast mold closing devices
4.Multi-stage and function ejection control and air blast fittings